The anaesthetic machine receives medical gases (oxygen, nitrous oxide, air) under pressure and provides a continuous and accurate flow of each gas individually. A gas mixture of the desired composition at a defined flow rate is created before a known concentration of an inhalational agent vapour is added. Gas and vapour mixtures are continuously delivered to the common gas outlet of the machine, as fresh gas flow (FGF), and to the breathing system and patient ( Figs 2.1 and 2.2 ). The anaesthetic machine consists of:
- 1.
gas supplies (see Chapter 1 )
- 2.
pressure gauges
- 3.
pressure regulators (reducing valves)
- 4.
flowmeters
- 5.
vaporizers
- 6.
a common gas outlet
- 7.
a variety of other features, e.g. high-flow oxygen flush, pressure-relief valve and oxygen supply failure alarm and suction apparatus


Most modern anaesthetic machines or stations incorporate a circle breathing system (see Chapter 4 ) and a bag-in-bottle type ventilator (see Chapter 8 ).
To ensure the delivery of a safe gas mixture safety features of a modern anaesthetic machine should include the following:
- •
colour-coded pressure gauges
- •
colour-coded flowmeters
- •
an oxygen flowmeter controlled by a single touch-coded knob
- •
oxygen is the last gas to be added to the mixture
- •
oxygen concentration monitor or analyser
- •
nitrous oxide is cut off when the oxygen pressure is low
- •
oxygen : nitrous oxide ratio monitor and controller
- •
pin-index safety system for cylinders and non-interchangeable screw thread (NIST) for pipelines
- •
alarm for failure of oxygen supply
- •
ventilator disconnection alarm
- •
at least one reserve oxygen cylinder should be available on machines that use pipeline supply
Pressure gauge
This measures the pressure in the cylinder or pipeline. The pressure gauges for oxygen, nitrous oxide and medical air are mounted in a front-facing panel on the anaesthetic machine ( Fig. 2.3 ).

Some modern anaesthetic machine designs have a digital display of the gas supply pressures ( Fig. 2.4 ).

Components
- 1.
A robust, flexible and coiled tube which is oval in cross-section ( Fig. 2.5 ). It should be able to withstand the sudden high pressure when the cylinder is switched on.
Fig. 2.5
The Bourdon pressure gauge.
- 2.
The tube is sealed at its inner end and connected to a needle pointer which moves over a dial.
- 3.
The other end of the tube is exposed to the gas supply.
Mechanism of action
- 1.
The high-pressure gas causes the tube to uncoil (Bourdon gauge).
- 2.
The movement of the tube causes the needle pointer to move on the calibrated dial indicating the pressure.
Problems in practice and safety features
- 1.
Each pressure gauge is colour-coded and calibrated for a particular gas or vapour. The pressure measured indicates the contents available in an oxygen cylinder. Oxygen is stored as a gas and obeys Boyle’s law (pressure × volume = constant). This is not the case in a nitrous oxide cylinder since it is stored as a liquid and vapour.
- 2.
A pressure gauge designed for pipelines should not be used to measure cylinder pressure and vice versa. This leads to inaccuracies and/or damage to the pressure gauge.
- 3.
Should the coiled tube rupture, the gas vents from the back of the pressure gauge casing. The face of the pressure gauge is made of heavy glass as an additional safety feature.
- •
Measures pressure in cylinder or pipeline.
- •
Pressure acts to straighten a coiled tube.
- •
Colour-coded and calibrated for a particular gas or vapour.
Pressure regulator (reducing valve)
Pressure regulators are used because:
- •
Gas and vapour are stored under high pressure in cylinders. A regulator reduces the variable cylinder pressure to a constant safer operating pressure of about 400 kPa (just below the pipeline pressure) ( Fig. 2.6 ).
Fig. 2.6
The principles of a pressure regulator (reducing valve).
- •
The temperature and pressure of the cylinder contents decrease with use. In order to maintain flow, constant adjustment is required in the absence of regulators.
- •
Regulators protect the components of the anaesthetic machine against pressure surges.
- •
The use of pressure regulators allows low-pressure piping and connectors to be used in the machine. This makes the consequences of any gas leak much less serious.
They are positioned between the cylinders and the rest of the anaesthetic machine ( Figs 2.7 and 2.8 ).


Components
- 1.
An inlet, with a filter, leading to a high-pressure chamber with a valve.
- 2.
This valve leads to a low-pressure chamber and outlet.
- 3.
A diaphragm attached to a spring is situated in the low-pressure chamber.
Mechanism of action
- 1.
Gas enters the high-pressure chamber and passes into the low-pressure chamber via the valve.
- 2.
The force exerted by the high-pressure gas tries to close the valve. The opposing force of the diaphragm and spring tries to open the valve. A balance is reached between the two opposing forces. This maintains a gas flow under a constant pressure of about 400 kPa.
Problems in practice and safety features
- 1.
Formation of ice inside the regulator can occur. If the cylinder contains water vapour, this may condense and freeze as a result of the heat lost when gas expands on entry into the low-pressure chamber.
- 2.
The diaphragm can rupture.
- 3.
Relief valves (usually set at 700 kPa) are fitted downstream of the regulators and allow the escape of gas should the regulators fail.
- 4.
A one-way valve is positioned within the cylinder supply line. This prevents backflow and loss of gas from the pipeline supplies should a cylinder not be connected. This one-way valve may be incorporated into the design of the pressure regulator.
- •
Reduces pressure of gases from cylinders to about 400 kPa (similar to pipeline pressure).
- •
Allows fine control of gas flow and protects the anaesthetic machine from high pressures.
- •
A balance between two opposing forces maintains a constant operating pressure.
Second-stage regulators and flow restrictors
The control of pipeline pressure surges can be achieved either by using a second-stage pressure regulator or a flow restrictor ( Fig. 2.9 ) – a constriction, between the pipeline supply and the rest of the anaesthetic machine. A lower pressure (100–200 kPa) is achieved. If there are only flow restrictors and no regulators in the pipeline supply, adjustment of the flowmeter controls is usually necessary whenever there is change in pipeline pressure.

Flow restrictors may also be used downstream of vaporizers to prevent back pressure effect (see later).
Flow control (needle) valves
These valves control the flow through the flowmeters by manual adjustment. They are positioned at the base of the associated flowmeter tube ( Fig. 2.10 ). Increasing the flow of a gas is achieved by turning the valve in an anticlockwise direction.

Components
- 1.
The body, made of brass, screws into the base of the flowmeter.
- 2.
The stem screws into the body and ends in a needle. It has screw threads allowing fine adjustment.
- 3.
The flow control knobs are labelled and colour-coded.
- 4.
A flow control knob guard is fitted in some designs to protect against accidental adjustment in the flowmeters.
Flowmeters
Flowmeters measure the flow rate of a gas passing through them. They are individually calibrated for each gas. Calibration occurs at room temperature and atmospheric pressure (sea level). They have an accuracy of about ± 2.5%. For flows above 1 L/min, the units are L/min, and for flows below that, the units are 100 mL/min ( Fig. 2.11 ).

Components
- 1.
A flow control (needle) valve.
- 2.
A tapered (wider at the top), transparent plastic or glass tube.
- 3.
A lightweight rotating bobbin or ball. Bobbin-stops at either end of the tube ensure that it is always visible to the operator at extremes of flow.
Mechanism of action
- 1.
When the needle valve is opened, gas is free to enter the tapered tube.
- 2.
The bobbin is held floating within the tube by the gas flow passing around it. The higher the flow rate, the higher the bobbin rises within the tube.
- 3.
The effect of gravity on the bobbin is counteracted by the gas flow. The pressure difference across the bobbin remains constant as it floats.
- 4.
The clearance between the bobbin and the tube wall widens as the gas flow increases ( Fig. 2.12 ).
Fig. 2.12
Mechanism of action of the flowmeter. As the bobbin rises from A to B , the clearance increases (from x to y ).
- 5.
At low flow rates, the clearance is longer and narrower, thus acting as a tube. Under these circumstances, the flow is laminar and a function of gas viscosity (Poiseuille’s law).
- 6.
At high flow rates, the clearance is shorter and wider, thus acting as an orifice. Here, the flow is turbulent and a function of gas density.
- 7.
The top of the bobbin has slits (flutes) cut into its side. As gas flows past it, the slits cause the bobbin to rotate. A dot on the bobbin indicates to the operator that the bobbin is rotating and not stuck.
- 8.
The reading of the flowmeter is taken from the top of the bobbin ( Fig. 2.13 ). When a ball is used, the reading is generally taken from the midpoint of the ball.
Fig. 2.13
Reading a flowmeter (top). Different types of bobbin: 1 , ball; 2 , non-rotating H float; 3 , skirted; 4 , non-skirted.
- 9.
When very low flows are required, e.g. in the circle breathing system, an arrangement of two flowmeters in series is used. One flowmeter reads a maximum of 1 L/min allowing fine adjustment of the flow. One flow control per gas is needed for both flowmeters ( Fig. 2.14 ).
Fig. 2.14
Two flowmeters in series.
- 10.
There is a stop on the oxygen flow control valve to ensure a minimum oxygen flow of 200–300 mL/min past the needle valve. This ensures that the oxygen flow cannot be discontinued completely.
Exam tip: Make sure you understand how the flowmeter works and the effects of viscosity and density on the function of the flowmeter.
Problems in practice and safety features
- 1.
The flow control knobs are colour-coded for their respective gases. The oxygen control knob is situated to the left (in the UK) and, in some designs, is larger with larger ridges and has a longer stem than the other control knobs so sticking out farthest, making it easily recognizable ( Fig. 2.15 ). In the United States and Canada, the oxygen control knob is situated to the right.
Fig. 2.15
Flow control knobs. Note the colour-coding and the distinctive-shape oxygen control knob.
- 2.
The European Standard for anaesthetic machines (EN 740) requires them to have the means to prevent the delivery of a gas mixture with an oxygen concentration below 25%. Current designs make it impossible for nitrous oxide to be delivered without the addition of a fixed percentage of oxygen. This is achieved by using interactive oxygen and nitrous oxide controls. This helps to prevent the possibility of delivering a hypoxic mixture to the patient. In the mechanical system, two gears are connected together by a precision stainless steel link chain. One gear with 14 teeth is fixed on the nitrous oxide flow control valve spindle. The other gear has 29 teeth and can rotate the oxygen flow control valve spindle, rather like a nut rotating on a bolt. For every 2.07 revolutions of the nitrous oxide flow control knob, the oxygen knob and spindle set to the lowest oxygen flow will rotate once. Because the gear on the oxygen flow control is mounted like a nut on a bolt, oxygen flow can be adjusted independently of nitrous oxide flow.
- 3.
A crack in a flowmeter may result in a hypoxic mixture ( Fig. 2.16 ). To avoid this, oxygen is the last gas to be added to the mixture delivered to the back bar.
Fig. 2.16
(A) A broken air flowmeter allows oxygen to escape and a hypoxic mixture to be delivered from the back bar. (B) A possible design measure to prevent this.
- 4.
Flow measurements can become inaccurate if the bobbin sticks to the inside wall of the flowmeter. The commonest causes are:
- a.
dirt: this is a problem at low flow rates when the clearance is narrow. The source of the dirt is usually a contaminated gas supply. Filters, acting before gas enters the flowmeters, will remove the dirt
- b.
static electricity: the charge usually builds up over a period of time, leading to inaccuracies of up to 35%. Using antistatic materials in flowmeter construction helps to eliminate any build-up of charge. Application of antistatic spray removes any charge present.
- a.
- 5.
Flowmeters are designed to be read in a vertical position, so any change in the position of the machine can affect the accuracy.
- 6.
Pressure rises at the common gas outlet are transmitted back to the gas above the bobbin. This results in a drop in the level of the bobbin with an inaccurate reading. This can happen with minute volume divider ventilators as back pressure is exerted as they cycle with inaccuracies of up to 10%. A flow restrictor is fitted downstream of the flowmeters to prevent this occurring.
- 7.
Accidents have resulted from failure to see the bobbin clearly at the extreme ends of the tube. This can be prevented by illuminating the flowmeter bank and installing a wire stop at the top to prevent the bobbin reaching the top of the tube.
- 8.
If facilities for the use of carbon dioxide are fitted to the machine, the flowmeter is designed to allow a maximum of 500 mL/min to be added to the FGF. This ensures that dangerous levels of hypercarbia are avoided.
- 9.
Highly accurate computer controlled gas mixers are available.
- •
Both laminar and turbulent flows are encountered, making both the viscosity and density of the gas relevant.
- •
The bobbin should not stick to the tapered tube.
- •
Oxygen is the last gas to be added to the mixture.
- •
It is very accurate with an error margin of ± 2.5%.
Vaporizers
A vaporizer is designed to add a controlled amount of an inhalational agent, after changing it from liquid to vapour, to the FGF. This is normally expressed as a percentage of saturated vapour added to the gas flow.
Characteristics of the ideal vaporizer
- 1.
Its performance is not affected by changes in FGF, volume of the liquid agent, ambient temperature and pressure, decrease in temperature due to vaporization and pressure fluctuation due to the mode of respiration.
- 2.
Low resistance to flow.
- 3.
Light weight with small liquid requirement.
- 4.
Economy and safety in use with minimal servicing requirements.
- 5.
Corrosion- and solvent-resistant construction.
Vaporizers can be classified according to location:
- 1.
Inside the breathing system. Gases pass through a very low resistance, draw-over vaporizer due to the patienťs respiratory efforts (e.g. Goldman, Oxford Miniature Vaporizer [OMV]). Such vaporizers are simple in design, lightweight, agent non-specific, i.e. allowing the use of any volatile agent, small and inexpensive. For these reasons, they are used in the ‘field’ or in otherwise difficult environments. However, they are not as efficient as the plenum vaporizers as their performance is affected as the temperature of the anaesthetic agent decreases due to loss of latent heat during vaporization.
- 2.
Outside the breathing system. Gases are driven through a plenum (high resistance, unidirectional and agent specific) vaporizer due to gas supply pressure. These vaporizers are reliable and easy to use.
Plenum vaporizer ( Fig. 2.17 )
Components
- 1.
The case with the filling level indicator and a port for the filling device.
- 2.
Percentage control dial on top of the case.
- 3.
The bypass channel and the vaporization chamber. The latter has Teflon wicks or baffles, cowls or nebulizers to increase the surface area available for vaporization ( Fig. 2.18 ).
Fig. 2.18
A schematic diagram of the Tec Mk 5, an example of a plenum vaporizer.
- 4.
The splitting ratio is controlled by a temperature-sensitive valve utilizing a bimetallic strip ( Fig. 2.19 ). The latter is made of two strips of metal with different coefficients of thermal expansion bonded together. It is positioned inside the vaporization chamber in the Tec Mk 2 whereas in Tec Mk 3, 4 and 5, it is outside the vaporization chamber. An ether-filled bellows is the temperature compensating device in the M&IE Vapamasta Vaporizer 5 and 6 (Key Health Solutions Ltd, Leicestershire, UK). The bellows contracts as the temperature of the vaporizer decreases.
Fig. 2.19
Mechanism of action of a bimetallic strip.Stay updated, free articles. Join our Telegram channel
Full access? Get Clinical Tree
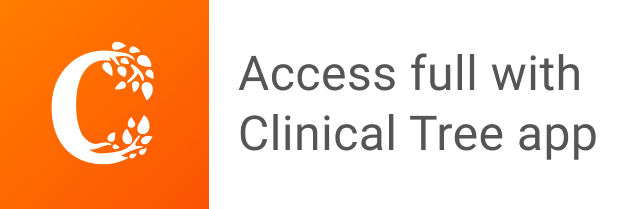