Chapter 95 Ropes and Knot Tying
Rope for Life Safety
Establishing and calculating an appropriate safety factor requires not only a fair amount of sophistication on the part of the user, but also a high starting strength to compensate for strength reductions as the equipment is integrated into a system. According to Cordage Institute specifications, static and low-stretch life-safety rope must meet the minimum strength requirement outlined in Table 95-1.
TABLE 95-1 Minimum Breaking Strength by Size (Diameter) Noted in Pounds-Force (lbf) and Kilonewtons (kN)
Diameter | Minimum Breaking Strength |
---|---|
7 mm (0.28 inch) | 2200 lbf (9.8 kN) |
8 mm (0.31 inch) | 2875 lbf (12.8 kN) |
10 mm (0.38 inch) | 4500 lbf (20.0 kN) |
11 mm (0.44 inch) | 6000 lbf (26.7 kN) |
12.5 mm (0.5 inch) | 9000 lbf (40.0 kN) |
16 mm (0.63 inch) | 12,500 lbf (55.6 kN) |
Number of Falls Held
Number of falls held applies only to dynamic climbing rope, on which falls are expected to be taken. To test for this, the impact force test described previously is repeated until the rope breaks. To qualify for Union of International Alpine Associations or European Committee for Standardization certification, a rope is required to sustain a minimum of five falls. The maximum number of falls achieved without breaking the rope is known as the fall rating. It is important to note that, for this test, the impact force requirement of 12 kN or less is measured only on the first fall. After the first fall, impact force is not measured and can be any force, as long as the rope does not break. This fall rating is basically used for comparison of one rope with another when purchasing a dynamic rope; it has little to do with the actual numbers of falls a given rope can take in the real world of climbing. A good-quality dynamic rope can provide good service for hundreds of low-impact falls. Alternatively, just because a rope is rated as something like 12 or 15 falls does not mean that it should be used over and over after an extremely high-impact fall has occurred (see Fall Factors, later, for information about estimating the impact of high-force falls on a rope).
Life-Safety Rope Construction
Rope Type
Dynamic Kernmantle Rope
Dynamic ropes also tend to have a lower tensile strength than do static or low-stretch kernmantle ropes because of the same design characteristics that allow it to stretch. Furthermore, dynamic kernmantle designs are often softer and have a lower percentage of sheath than do static kernmantle ropes, making them more susceptible to abrasion and wear (Figure 95-1).
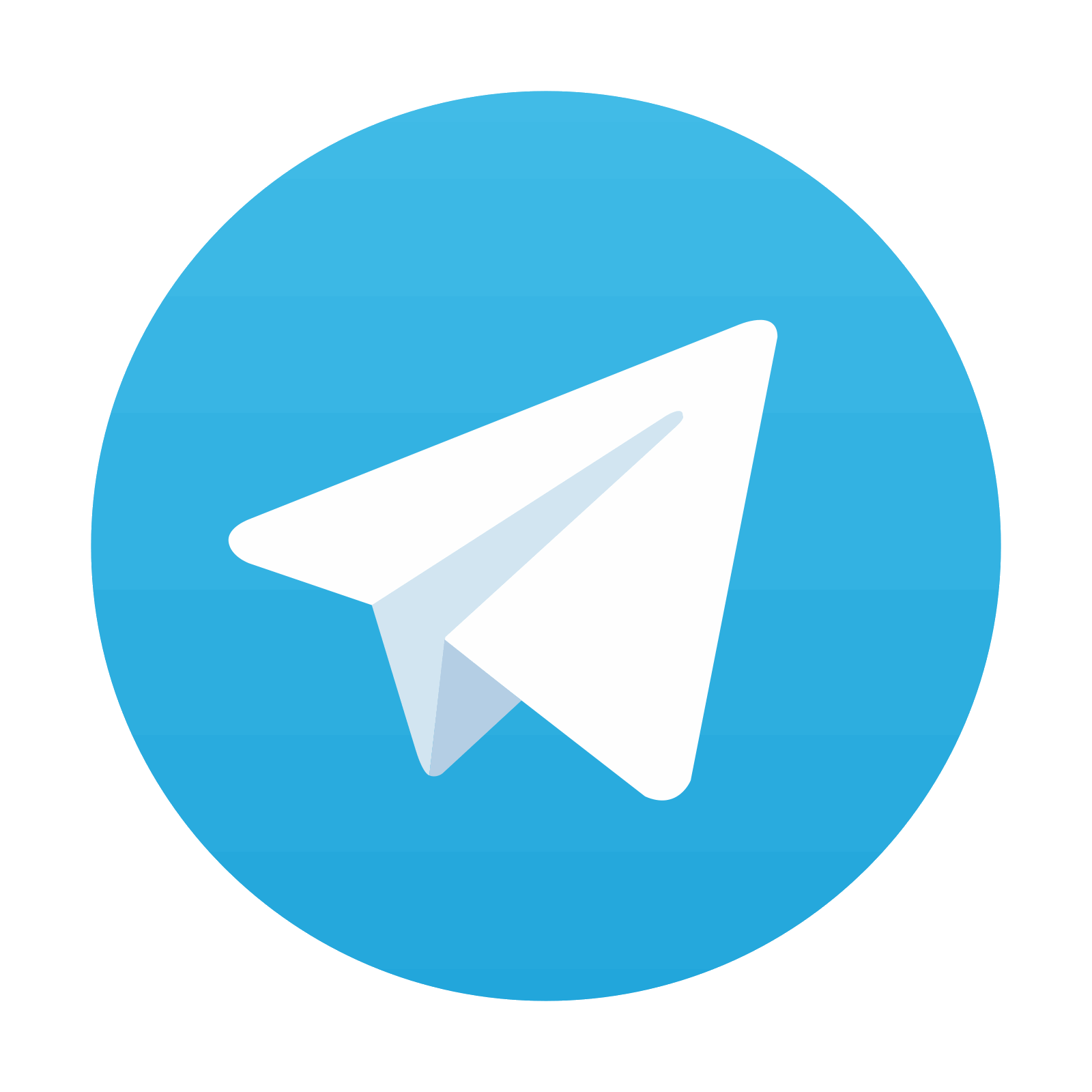
Stay updated, free articles. Join our Telegram channel
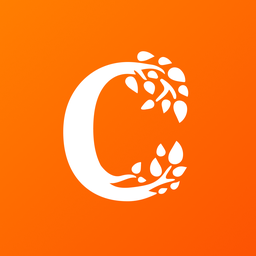
Full access? Get Clinical Tree
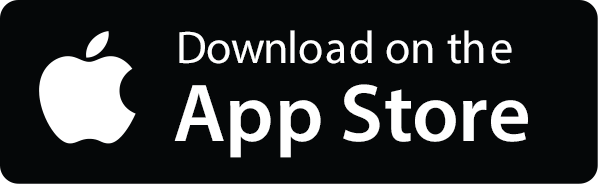
